An overview of types of steel
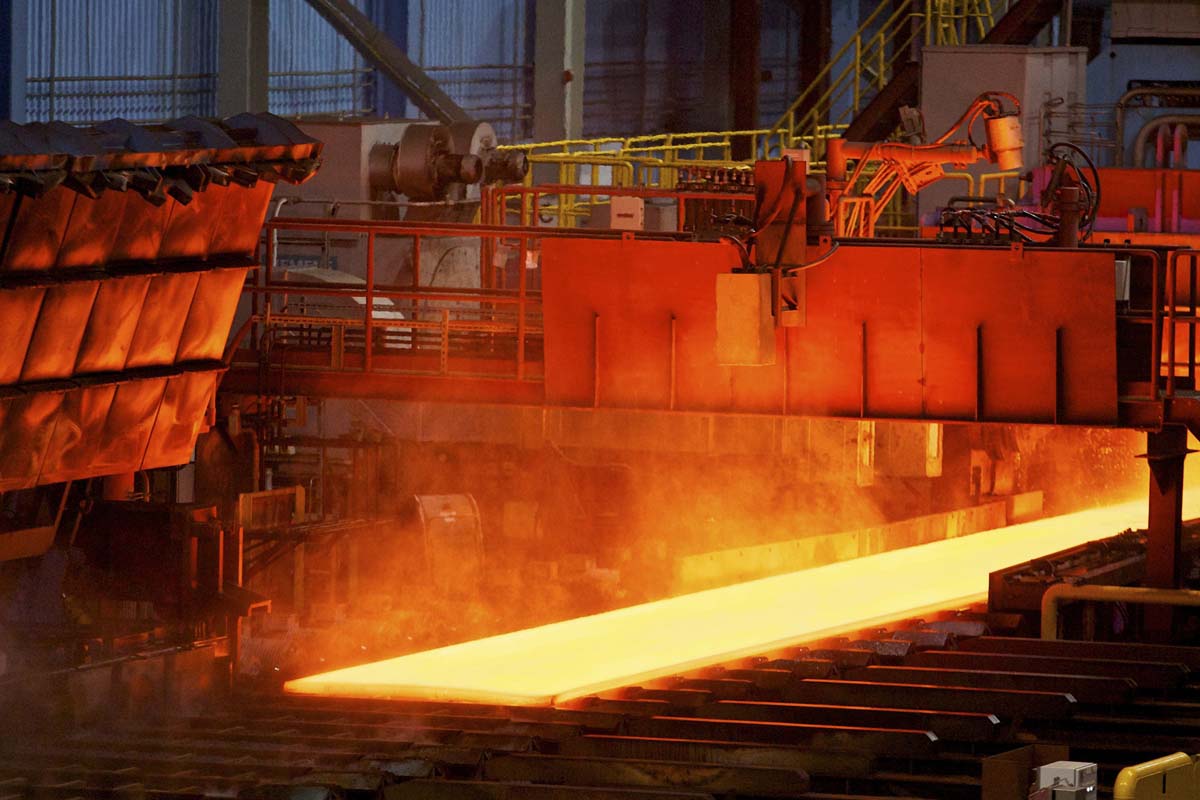
The total number of existing steels is over a thousand types, but their composition and other variables cannot be determined exactly, but according to the convention, steels are divided into five categories: these five categories are: carbon steel, alloy steel, stainless steel Stainless steel, tool steel, and special steel, the first four categories in […] […]
The total number of existing steels is over a thousand types, but their composition and other variables cannot be determined exactly, but according to the convention, steels are divided into five categories: these five categories are: carbon steel, alloy steel, stainless steel Stainless steel, tool steel, and special steel, the first four categories in […]
The total number of existing steels is over a thousand types, but their composition and other variables cannot be determined exactly, but according to the convention, steels are divided into five categories: these five categories are: carbon steel, alloy steel, stainless steel Stainless steel, tool steel, and special steel of the first four categories are specified in the American Iron and Steel Institute (AISI) standard and include subgroups, but the steels of the fifth category have different compositions and are completely specific, however, many of these steels They have the same composition as other steels. For example, the AISI standard specifies about 75 types of stainless steel, which are divided into four standard groups. In addition to this number, there are at least a hundred other types of compositions that are non-standard, but for special purposes. have been developed
All steels are simple or complex combinations of iron and carbon alloys. All plain carbon steels contain certain percentages of manganese and silicon plus very small amounts of phosphorus and sulfur.
For example, the nominal composition of AISI or SAE standard 1045 steel may contain 0.45 carbon; 0.75 manganese, 0.040 phosphorus, 0.050 sulfur and 0.22 sulfur. Alloy steels are another category of steels that have other elements in their chemical composition.
The most elements used in the composition of alloy steels are: nickel, chromium, molybdenum, vanadium and tungsten.
When the percentage of manganese is more than one percent, this element is also considered as an alloy element. To achieve the desired properties of steel in engineering applications, one or more of the above elements are added to steel.
Carbon element is the main element in all steels; So, the amount of carbon in plain carbon steels has a great influence on the properties of the steel and the selection of the appropriate heat treatment for the steel. This operation is performed in order to obtain desirable properties on steel.
Due to the importance of carbon content in steels, one of the classifications of simple carbon steels is based on their carbon content. When only a small amount of carbon is present in steel, that steel is called low carbon or soft steel. If the amount of carbon is less than 0.30% by weight of steel, it is called low carbon steel. If the carbon content of steel is approximately 0.30% to 0.60% by weight, it is included in the group of medium carbon steels, and steels with more than 0.60% carbon by weight are called high carbon steels, if the carbon content of the steel is more from 0.77 percent by weight, they are called tool steels. The carbon content of steel is rarely between 1.3 and 2%.
The maximum amount of carbon in steel is approximately 2%, and when the amount of carbon is more than this, it is called a cast iron alloy. The amount of carbon in cast iron is usually between 2.3 and 4%. Cast irons are an important group of casting alloys.
Different steels have different properties in terms of the amount and type of heat treatment that is done on them.
In the heat treatment of steel, one of the following goals is usually followed:
- Stress relief from etching or stress relief from heterogeneous cooling
- Optimizing grain structure in steels that have been hot worked and may have coarse grains.
Optimization of grain structure
- Reducing steel hardness and increasing malleability
- Increasing the hardness of steel in order to increase wear resistance or to harden steel for greater resistance in working conditions
- Increasing the toughness of steel in order to produce steel that has high strength and good flexibility and increasing the resistance of steel against impact
- Improvement of machinability
- Improvement of cutting properties in tool steels
- Optimizing the magnetic properties of steel
- Improving the electrical properties of steel
Some of these operations are as follows:
TEMPERING
Malleability is the change of shape of the steel before the fracture of the quenched martensite, which is hard and non-malleable.
To improve the malleability of martensite, it should be annealed, although in this case its strength will decrease a little. On the other hand, annealing increases the resistance of martensite against sudden impact. For example, if a hammer is quenched, its structure becomes completely martensitic, which is likely to crack after the first blows. But by using the annealing operation, the impact of the hammer increases (the brittleness decreases) and instead the hardness and strength of the hardened part will decrease to some extent, the annealing operation is such that the rapidly cooled part is brought to a temperature below the heat transfer temperature. and then keep at this temperature for an hour or more depending on the size of the piece. Most steels are annealed at a temperature of 400 to 1100 (205 to 959). The higher the annealing temperature, the higher the toughness and impactability of the steel. Instead, its hardness and strength will decrease. The destruction of needle-shaped martensite and the deposition of very fine carbide particles are among the structural changes during annealing. Microscopic structure of quenched and annealed steels are introduced as annealed martensite.
Anil
Rapid cooling heat treatment and then annealing of steel increases its strength, malleability and impact resistance. The science of machining and bending is used in the manufacture of most steel products, so in order to improve the machining properties and the ability to change the shape of steel, it is annealed. Even in some cases, machining and bending of annealed parts is also difficult. To solve this problem, the parts are annealed.
Normalization
The homogenization process consists of heating the piece to a high temperature and then cooling it in the open air. The necessary temperature of homogenization depends on the composition of the steel, which is usually around 1600 (870). The homogenization process is known as homogenization or nucleation. In each piece of steel, the composition is usually not uniform on all surfaces. This means that the amount of carbon in one part of the steel may be higher than other parts. These compositional differences affect the heat treatment of steel. If the steel is heated at a high temperature, the carbon can easily have a uniform composition on the entire surface of the steel, in this case the steel becomes more homogeneous and is better prepared for heat treatment. Due to the properties of castings, ingots are usually homogenized before use. In the same way, cast and forged steels are homogenized before hardening.
De-stressing
When the metal is heated at a high temperature, the metal expands, and on the contrary, when the metal is cooled from a high temperature, it contracts. During forge welding, when one part of the steel tube or sheet is heated more than the other parts, a lot of internal stress occurs in the steel. As the steel heats up, the expanded parts have nowhere to settle, so the part changes shape. During cooling, the contraction of the piece prevents the formation of cold and hard metal around the heat zone. The forces that have arisen in the piece during the contraction have not been released yet, and when the metal cools again, these forces remain as internal stresses. . Internal stresses also arise as a result of volume changes and transfer and deposition of metal.
The term stress is widely used in the field of metallurgy and it is the load of force that is applied to the cross section of steel. Internal stresses and residual stresses are harmful to steel because they may cause cracks while the steel is being machined. To release these stresses, the steel is heated to a temperature of about 1100 (595), until they are sure that all parts of the steel have been heated uniformly, then they cool it slowly to room temperature. These steps are called annealing or just the same. It is called de-stressing.
Effective parameters on hardenability
If the hardenability of a steel is high, even in relatively slow cooling rates, the intrusive transformation of pearlite formation is not done and austenite turns into martensite. On the contrary, in steels with low hardenability, the formation of martensite requires rapid cooling. In both cases, the limiting parameter is the rate of pearlite formation at high temperatures. In general, any factor that shifts the lines of pearlite formation in the CCT diagram to the right allows the formation of martensite at lower cooling rates. Therefore, the shift of the nose of the CCT diagram to the right is accompanied by an increase in hardness. In other words, any factor that reduces the rate of germination and growth of pearlite (increases the time for germination and growth of pearlite) increases the hardenability in steels. These factors include:
Hardness and toughness
Martensitic microstructure is the hardest microstructure that can be formed in a plain carbon steel. The formation of martensitic microstructure is possible if the transformation of austenite to a mixture of ferrite and cementite is prevented at high temperatures.
Austenite grain size
Since with the falling of the grains, the total surfaces related to the grain boundaries increase in a steel with fine grains, the formation of pearlite is much faster than a steel with coarse grains. As a result, the hardenability of steel with fine grains will be lower than the hardenability of steel with coarse grains. But the use of steel with coarse grains in order to increase the hardness is practically not used in industry, because increasing the hardness of this method is associated with unwanted and harmful changes in the properties of steel, such as increasing brittleness and reducing flexibility. Among the other defects that occur mostly in coarse grain steels are: cracks caused by rapid cooling or cracks caused by thermal shocks caused by the stresses resulting from heat treatment.